Exploring the World of Pressure Die Casting Products
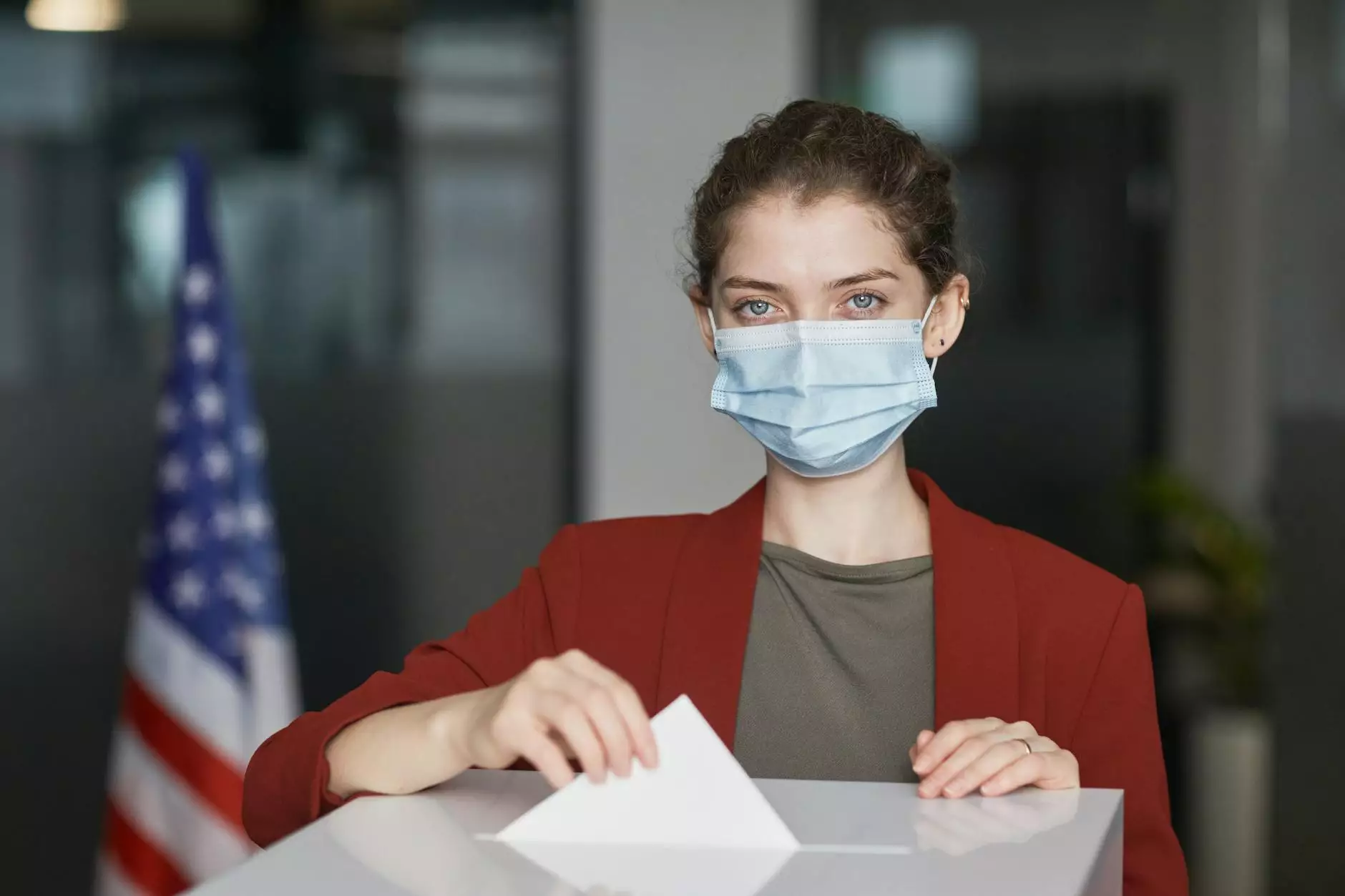
The manufacturing industry has consistently evolved, embracing innovative techniques to meet the ever-growing demand for high-quality metal components. Among these techniques, pressure die casting has emerged as a pivotal process, enabling the production of intricate and durable products. In this comprehensive article, we dive deep into the realm of pressure die casting products, elucidating their advantages, processes, applications, and the future of this essential manufacturing method.
What is Pressure Die Casting?
Pressure die casting is a manufacturing process that involves forcing molten metal under high pressure into reusable molds, known as dies. The process is primarily used for metals with low melting points, like aluminum, zinc, and magnesium. This method is renowned for producing a variety of complex shapes with excellent surface finishes and dimensional accuracy.
Key Advantages of Pressure Die Casting
Understanding the benefits of pressure die casting products can shed light on why this technique is prevalent in the automotive, aerospace, and electronics industries, among others. Here are some noteworthy advantages:
- Precision and Accuracy: The use of high pressure ensures that the molten metal fills the die completely, resulting in finished products that meet stringent tolerances.
- Efficiency: Pressure die casting provides a rapid production cycle, allowing for the manufacturing of large volumes of parts in a short timeframe.
- Excellent Surface Finish: The process often results in a smooth surface finish that typically does not require any further machining.
- Material Savings: Minimal waste is generated in pressure die casting, as the process allows for the reuse of excess metal.
- Versatility: This casting method permits the use of a variety of metals, which can be selected based on desired properties like strength, weight, and corrosion resistance.
The Pressure Die Casting Process Explained
To appreciate the significance of pressure die casting products, it is essential to understand the steps involved in the process. The following is a detailed breakdown:
1. Mold Creation
The first step involves designing and manufacturing a die from steel or iron. The die is precisely machined to form the negative shape of the final product. High-quality dies aim to withstand the high pressures and temperatures involved in the casting process.
2. Melting the Metal
The metal is then heated in a furnace until it reaches a molten state. The choice of metal is crucial, as it influences the final properties of the pressure die casting products.
3. Injection of Molten Metal
Once the metal is molten, it is injected into the die at high speed and pressure. This ensures complete filling of the cavity, which is critical in achieving accurate and high-quality castings.
4. Cooling and Solidification
After the metal fills the die, it is allowed to cool and solidify. This stage is crucial, as the rate of cooling can affect the properties of the final product.
5. Ejection
Once the metal has solidified, the die opens, and ejector pins remove the casting from the mold. Care must be taken during this step to avoid damage to the finished product.
Applications of Pressure Die Casting Products
The versatility of pressure die casting products leads to their application across various sectors. Below are some common industries that benefit from this manufacturing process:
1. Automotive Industry
The automotive sector relies heavily on pressure die casting for producing components like engine blocks, transmission cases, and decorative elements. The durability and lightweight nature of the cast parts contribute significantly to the overall efficiency of vehicles.
2. Aerospace Industry
In aerospace, precision and reliability are paramount. Pressure die casting products are utilized in crafting critical components such as fuel pumps, housings, and brackets, enabling manufacturers to meet strict regulatory standards while reducing weight.
3. Electronics Industry
Many electronic devices utilize pressure die casting for their housings and internal components. The excellent thermal and electrical conductivity of metals ensures efficient performance and longevity.
Future Trends in Pressure Die Casting
The future of pressure die casting products appears promising, buoyed by advancements in technology and increasing demand across various industries. Below are trends shaping the future landscape:
1. Automation and Robotics
With the advent of Industry 4.0, automation and robotics are being integrated into die casting operations. This shift enhances efficiency, reduces human error, and allows for more consistent product quality.
2. Advanced Materials
The exploration of new metal alloys is paving the way for stronger and lighter pressure die casting products. Manufacturers are increasingly experimenting with composite materials to enhance performance while reducing costs.
3. Sustainability Initiatives
As industries worldwide focus on sustainability, pressure die casting companies are adopting greener practices. This includes recycling waste materials and using energy-efficient furnaces, thereby minimizing their environmental footprint.
The Importance of Working with Quality Suppliers
Choosing the right supplier for pressure die casting products is paramount to ensuring quality and reliability. Here are some factors to consider when selecting a partner:
- Experience: Look for suppliers with a proven track record in the die casting industry.
- Certifications: Verify that the supplier adheres to industry standards such as ISO certification.
- Capability: Ensure the supplier can meet your specific requirements in terms of quantity, material, and complexity of design.
- Technology: Evaluate the technology and machinery used by the supplier, as this can significantly impact the quality of the products.
Conclusion
In conclusion, pressure die casting products play an integral role in the modern manufacturing landscape. With their unparalleled precision, efficiency, and versatility, they continue to drive innovation across multiple industries. As companies like DeepMould leverage these advantages, the future of pressure die casting is poised for significant growth and advancement. Emphasizing quality, collaboration, and technological innovation will be key to maintaining leadership in this dynamic industry.