Comprehensive Guide to Profile in PVC: Strength, Versatility, and Sustainability
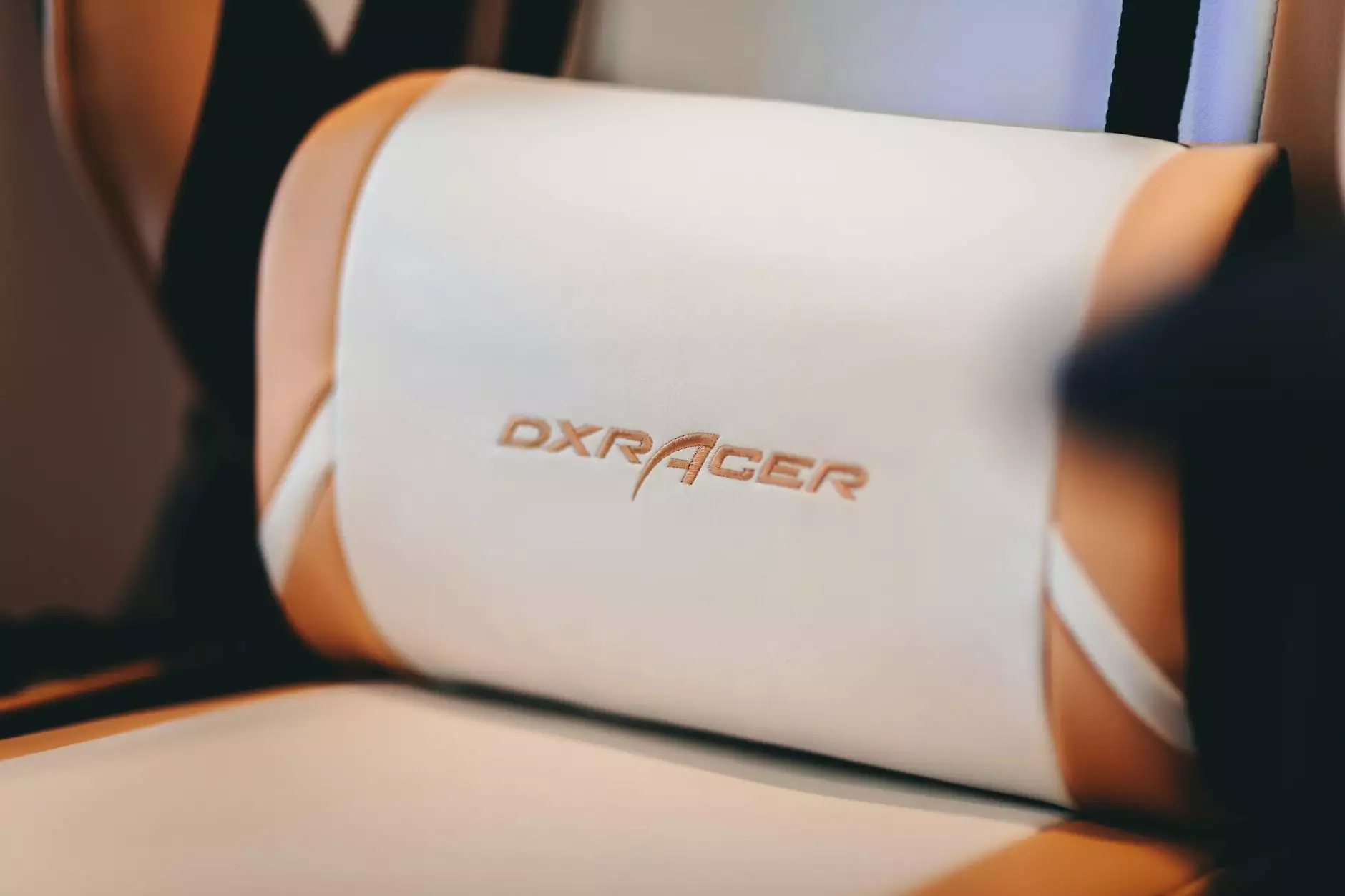
Profile in PVC has become an integral part of various industries due to its outstanding qualities and versatility. Whether it's in construction, automotive, or the manufacturing of home products, PVC has established itself as a material of choice. In this article, we will delve deep into the numerous benefits, applications, and manufacturing processes of PVC profiles, particularly highlighting the offerings of Hidroplasto, a leading manufacturer in this domain.
The Advantages of Using Profile in PVC
When discussing polymers, it's essential to highlight why PVC (polyvinyl chloride) has gained such popularity. Here are some compelling advantages:
- Durability: PVC is known for its exceptional durability and resilience. It is resistant to corrosion, aging, and weather elements, making it suitable for outdoor applications.
- Low Maintenance: PVC profiles are easy to maintain due to their ability to resist dirt and discoloration. A simple wash with soap and water can keep them looking new.
- Eco-Friendly: As a recyclable material, PVC promotes sustainability. Manufacturers like Hidroplasto use eco-friendly techniques to create products that can be recycled at the end of their life cycle.
- Cost-Effective: Profile in PVC offers a budget-friendly option compared to other materials without compromising on quality.
- Versatility: The adaptability of PVC allows for its application in different fields, including window frames, doors, plumbing systems, and flooring.
Understanding the Manufacturing Process of PVC Profiles
The creation of PVC profiles involves a sophisticated manufacturing process that ensures high quality and performance. Below is an overview of the steps involved:
1. Raw Material Selection
The first step in manufacturing PVC profiles is selecting high-quality raw materials. The primary component is polyvinyl chloride resin, which is usually combined with various additives to enhance performance characteristics such as flexibility, UV stability, and color pigmentation.
2. Compounding
The selected raw materials are compounded in an extruder. In this process, heat is applied to melt the PVC and mix it with additives thoroughly. This results in a homogenous material that maintains consistent quality throughout.
3. Extrusion
The compounded PVC is then forced through a die in the extrusion process, which shapes the material into continuous profiles. This step is crucial as it defines the dimensions and technical specifications of the end product.
4. Calibration and Cooling
Once extruded, the profiles are calibrated and cooled. This ensures precise dimensions, and the profiles are passed through cooling tanks or air-cooled systems to solidify.
5. Cutting and Finishing
After cooling, the profiles are cut to required lengths. Additional finishing touches may involve surface treatments or the application of decorative layers, depending on the intended application.
Applications of Profile in PVC
PVC profiles have a wide range of applications thanks to their remarkable properties. Below are some notable uses:
1. Construction Industry
In construction, PVC profiles are widely used for window frames, doors, and roofing materials. Their thermal insulation properties contribute to energy-efficient buildings.
2. Furniture Industry
PVC profiles are utilized in furniture manufacturing, particularly for components like edge banding and frame structures. They offer design flexibility and aesthetic appeal.
3. Electrical Installations
Electrical conduits made from PVC protect wiring and are resistant to moisture, making them ideal for residential and commercial electrical installations.
4. Medical Applications
In the medical industry, PVC profiles can be found in a range of applications, such as tubes and containers due to their hygiene and safety properties.
Innovations in PVC Manufacturing by Hidroplasto
Hidroplasto stands out as a leader in the PVC manufacturing sector, renowned for their dedication to quality and innovation. They are constantly pushing the boundaries in terms of:
- Advanced Technology: Utilizing modern manufacturing technologies, they ensure that every profile in PVC meets or exceeds industry standards.
- Customization: Offering tailored solutions, Hidroplasto can create profiles that meet specific customer requirements for shape, size, and performance.
- Sustainability Practices: Adopting eco-friendly practices, they minimize waste and improve recyclability, aligning with global sustainability goals.
- Research and Development: Continuous investment in R&D allows Hidroplasto to innovate and bring the latest advancements in PVC technology to their products.
The Future of PVC Profiles
The future of profile in PVC is promising and vibrant. As industries continue to evolve, the demand for durable, flexible, and eco-friendly materials is on the rise. Innovations in manufacturing techniques and material science will likely lead to improved formulations that enhance performance.
Conclusion
In summary, the profile in PVC represents a cornerstone of modern manufacturing solutions across various industries. With its advantageous properties, cost-effectiveness, and versatility, it has proven to be an invaluable material. Companies like Hidroplasto exemplify the quality and innovation the PVC manufacturing sector can achieve. As we move forward, embracing these materials will be crucial for sustainable development and functional design.
By investing in PVC technology, industries are not only ensuring longevity and performance but also contributing to a more sustainable future.