Hydraulic Tube Fittings Manufacturer: Quality and Innovation
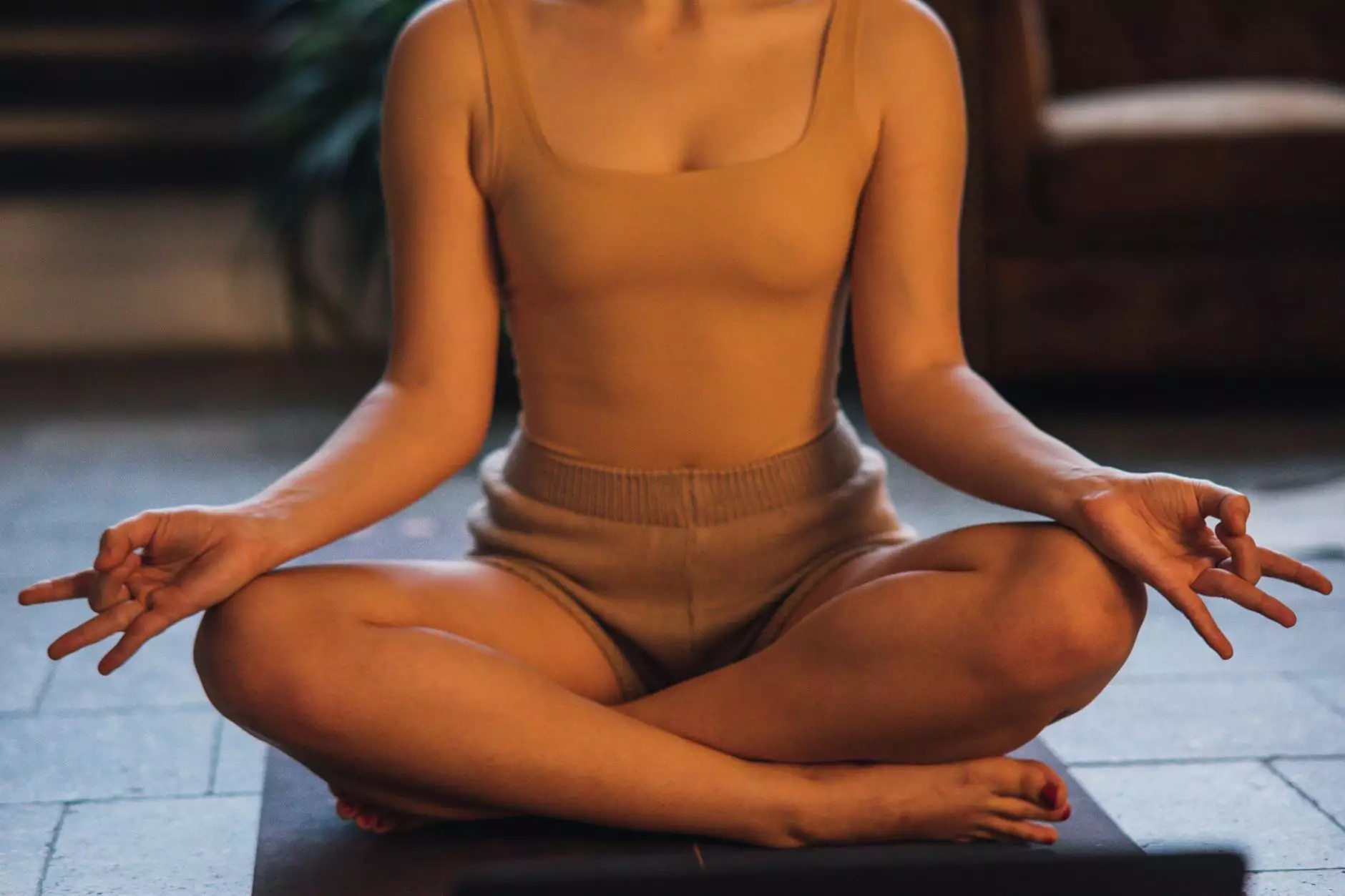
In the dynamic world of manufacturing, becoming a leading Hydraulic Tube Fittings Manufacturer is no small feat. With the increasing demand for reliable and efficient hydraulic solutions across various industries, manufacturers must prioritize quality, precision, and innovation. This article delves deep into the sphere of hydraulic tube fittings, exploring not just the products but also the processes that make a manufacturer stand out in this competitive market.
Understanding Hydraulic Tube Fittings
Hydraulic tube fittings are crucial components in hydraulic systems, serving to connect tubes, pipes, or hoses in a secure and reliable manner. They are designed to withstand high pressures and are used in applications ranging from industrial machinery to automotive systems. Understanding the different types of hydraulic tube fittings is essential for selecting the right products for specific applications.
Types of Hydraulic Tube Fittings
- Compression Fittings: These fittings create a tight seal by compressing the tubing or pipe against a ferrule.
- BSP Fittings: British Standard Pipe fittings are commonly used in fluid and gas applications.
- NPT Fittings: National Pipe Tapered fittings are used in the U.S. for oil and gas applications.
- Flared Fittings: Ideal for high-pressure applications, these fittings create a flare at the end of the tube for a secure connection.
- Welded Fittings: These fittings are permanently attached to the pipe or tube via welding, ensuring a robust connection.
Why Choose a Quality Hydraulic Tube Fittings Manufacturer?
Choosing a reliable hydraulic tube fittings manufacturer is pivotal for any business looking to enhance its productivity and operational safety. The right manufacturer not only provides high-quality products but also delivers exceptional service and support.
Key Considerations When Selecting a Manufacturer
- Quality Assurance: It is vital to ensure that the manufacturer follows stringent quality control processes. Look for certifications such as ISO 9001, which indicates a commitment to quality management standards.
- Material Selection: The materials used in manufacturing fittings affect their durability and performance. High-grade stainless steel, brass, and carbon steel are often preferred.
- Innovation: A manufacturer committed to research and development will consistently evolve their product offerings, ensuring they meet modern challenges.
- Customization: Depending on specific operational needs, having the option for customized fittings is a valuable asset.
- After-Sales Support: Reliable customer service and technical support should be part of the package. A manufacturer should provide assistance even after the sale is complete.
The Manufacturing Process Behind Hydraulic Tube Fittings
Understanding the manufacturing process helps to appreciate what goes into producing high-quality hydraulic tube fittings. Each step is critical in ensuring the final product meets industry standards.
Step 1: Material Procurement
The first step in the manufacturing process is the procurement of raw materials. Quality materials ensure that the fittings are durable and reliable. Manufacturers like fitsch.cn source materials that comply with international standards.
Step 2: Machining
Once the materials are obtained, they undergo machining processes, including cutting, shaping, and forming. This stage is essential for achieving precise dimensions and tolerances that hydraulic fittings require.
Step 3: Assembly
After machining, the components are assembled. This step may involve press-fitting, welding, or the use of adhesives, depending on the type of fitting being produced. Each assembly method must ensure a leak-proof connection.
Step 4: Quality Control
Rigorous testing is conducted to guarantee that each fitting can withstand the pressures and conditions it will encounter in its operational environment. Tests may include pressure testing, leak testing, and dimensional inspections.
Step 5: Surface Treatment
Finally, surface treatments such as plating or coating may be applied to enhance corrosion resistance and improve the aesthetic appearance of the fittings.
The Role of Technology in Hydraulic Tube Fittings Manufacturing
Technology is reshaping the manufacturing landscape, and hydraulic tube fittings production is no exception. Advanced technologies in machining, automation, and logistics are enhancing production efficiency and product quality.
Modern Machining Techniques
CNC (Computer Numerical Control) machining allows for precise and consistent manufacturing of fittings. With CNC technology, manufacturers can produce complex shapes with high accuracy, significantly reducing waste and rework.
Automation and Robotics
Integrating automation into the manufacturing process improves efficiency and safety. Robotic systems can perform repetitive tasks, freeing human operators for more complex problem-solving roles.
Supply Chain Integration
Implementing advanced data analytics and inventory management systems ensures that the right materials are available when needed, further optimizing the production timeline.
Applications of Hydraulic Tube Fittings
Hydraulic tube fittings serve a vital role across numerous sectors. Understanding these applications can help potential customers appreciate their importance.
Industrial Machinery
In industrial settings, hydraulic fittings are used in machinery such as pumps, presses, and forklifts. Reliable fittings ensure machinery operates efficiently and safely.
Aerospace and Defense
Hydraulic systems in aircraft and defense vehicles demand high-performance fittings due to the extreme conditions they face. Quality assurance in this sector is critical.
Automotive Industry
Automobiles rely on hydraulic systems for braking, steering, and suspension. Therefore, high-quality fittings are essential for vehicle safety and performance.
Construction and Mining
Heavy equipment used in construction and mining operations depends on hydraulic systems. Durable fittings guarantee that these machines operate efficiently under tough conditions.
Conclusion
As a leader in the field, fitsch.cn exemplifies what it means to be a top-tier Hydraulic Tube Fittings Manufacturer. With a strong commitment to quality, innovation, and customer service, manufacturers can not only meet but exceed the expectations of their clientele. The future of hydraulic fittings manufacturing is bright, with continued advancements set to enhance both product offerings and operational efficiencies.
FAQs about Hydraulic Tube Fittings
What materials are hydraulic tube fittings made from?
Common materials include stainless steel, brass, and carbon steel, depending on the application requirements and environmental conditions.
How do I choose the right fitting for my application?
Consider factors like pressure ratings, the type of fluid being transported, and compatibility with existing systems to select the right fitting.
Can hydraulic tube fittings be modified?
Yes, many manufacturers offer customization options to adapt fittings for specific applications or performance requirements.
What is the importance of quality control in manufacturing hydraulic fittings?
Quality control is essential to ensure the fittings can withstand the operational pressures and conditions without failure, thereby safeguarding system integrity and safety.
Hydraulic Tube Fittings Manufacturer