Understanding the Role of Precision Components Manufacturers
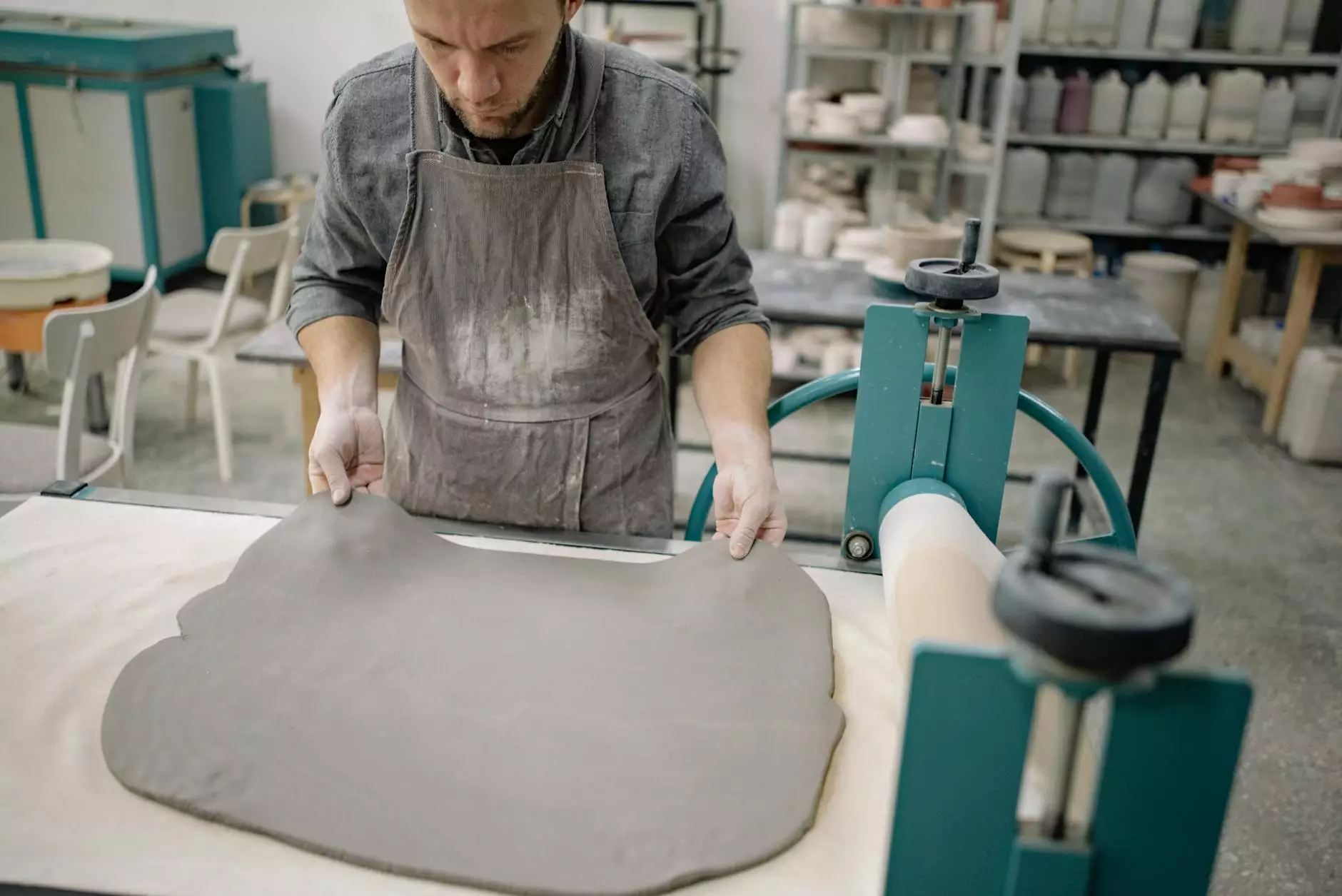
In today's rapidly evolving technological landscape, the importance of precision components manufacturers cannot be overstated. These manufacturers are the backbone of many modern industries, providing essential components that ensure the functionality and reliability of various products. From aerospace and automotive to medical devices and electronics, the need for precision in component manufacturing is paramount to achieving high standards of quality and efficiency.
The Significance of Precision in Manufacturing
Precision in manufacturing refers to the ability to produce components that meet strict tolerances and specifications. This is crucial for ensuring that parts fit together correctly, function as intended, and maintain durability over time. In many industries, even the slightest deviation can lead to significant failures, safety hazards, and increased costs.
Industries Dependent on Precision Components
The reach of precision components manufacturers is vast, impacting numerous industries. Here are some of the key sectors that rely heavily on precision manufacturing:
- Aerospace: Components must meet stringent regulatory standards for safety and performance.
- Automotive: Precision parts ensure high performance and emission standards in vehicles.
- Medical Devices: Precision is critical in devices that save lives, such as surgical instruments and diagnostic equipment.
- Electronics: High-tech devices need intricate components that follow exact specifications.
- Defense: Components must be reliable and durable under extreme conditions.
The Manufacturing Processes Utilized by Precision Components Manufacturers
The journey of creating precision components involves several sophisticated manufacturing processes. Here are some of the most prevalent ones:
1. CNC Machining
CNC (Computer Numerical Control) machining uses computers to control machine tools. This automation allows for high precision and accuracy, enabling manufacturers to produce intricate designs with repeatable quality.
2. Injection Molding
Commonly used for producing plastic parts, injection molding allows for high-volume production and complex geometries, making it a staple in the manufacturing of components across various sectors.
3. Sheet Metal Fabrication
This process involves cutting, bending, and assembling metal sheets to create precise components. Techniques like laser cutting and welding ensure the quality and accuracy required in precision manufacturing.
4. 3D Printing
Also known as additive manufacturing, 3D printing is becoming increasingly popular for prototyping and producing complex structures with minimal waste, allowing for rapid iteration and design flexibility.
5. Surface Treatment
Surface treatments such as anodizing, plating, and coating enhance the physical and chemical properties of components, ensuring long-lasting durability and performance.
The Benefits of Partnering with Precision Components Manufacturers
Businesses across different sectors stand to gain significantly by collaborating with precision components manufacturers. Here are some of the benefits:
- Quality Assurance: These manufacturers undergo rigorous quality checks at every stage of the production process, ensuring that only the best products reach the end-user.
- Cost Efficiency: By optimizing manufacturing processes and reducing waste, precision manufacturers can offer competitive pricing without compromising on quality.
- Innovation: Many precision manufacturers invest in cutting-edge technology and R&D, offering innovative solutions that can enhance product performance.
- Customization: Precision manufacturers often provide tailored solutions that meet the unique needs of each client, allowing for greater flexibility in product development.
- Shorter Lead Times: With advanced manufacturing techniques, precision manufacturers can produce components faster, helping businesses reduce their time to market.
How to Choose the Right Precision Components Manufacturer
Selecting the right manufacturer is a critical decision for any business. Here are some factors to consider when choosing a precision components manufacturer:
1. Experience and Expertise
It's essential to evaluate the manufacturer’s experience in producing the specific components you need. Look for a company with a proven track record in your industry.
2. Technology and Capabilities
Ensure that the manufacturer has up-to-date technology and the necessary capabilities to meet your production requirements, including handling complex designs and large volumes.
3. Quality Control Processes
Inquire about the quality control measures in place. An effective quality management system will help guarantee that the components are produced to the highest standards.
4. Communication and Support
Choose a manufacturer that offers strong customer support and clear communication channels. Being able to collaborate effectively is vital for successful project outcomes.
5. References and Reputation
Finally, consider reviews and testimonials from other clients. A manufacturer with a strong reputation in the industry is likely to deliver better results.
Future Trends in Precision Component Manufacturing
The manufacturing landscape is continuously evolving. Here are some future trends that are likely to shape the field of precision components manufacturers:
1. Automation and Robotics
With advancements in robotics and automation, factories are becoming smarter and more efficient. This trend is expected to enhance production rates, reduce errors, and improve overall quality.
2. Digital Twin Technology
This technology allows manufacturers to create virtual models of physical products. By simulating real-world performance, manufacturers can optimize the design before production, reducing costs and improving outcomes.
3. Sustainable Manufacturing
With the increasing emphasis on sustainability, precision component manufacturers are looking for ways to minimize their environmental impact through eco-friendly practices and materials.
4. Industry 4.0
The integration of IoT (Internet of Things) and big data into manufacturing processes is paving the way for smart manufacturing, whereby real-time data enhances decision-making and efficiency.
5. Advanced Materials
The development of new materials, such as composites and smart materials, is broadening the horizons of what precision components can achieve, leading to the creation of lighter, stronger, and more adaptable products.
Conclusion
The role of precision components manufacturers in the modern industrial landscape is vital. They not only support the production of high-quality components across various sectors but also drive innovation and sustainability in manufacturing practices. As industries continue to advance, the importance of these manufacturers will only increase, making it crucial for businesses to choose their partners wisely to stay competitive in an ever-evolving market.
At DeepMould.net, we are committed to delivering unparalleled quality in precision components manufacturing. Our extensive experience, state-of-the-art technology, and dedication to client satisfaction make us a leader in the field.